From elegant classics to innovative modern designs, faucets play an important role in enhancing the ambiance and practicality of our homes. Have you ever wondered about the manufacturing process behind these products?
In this article, we’ll take a deep dive into the fascinating world of faucet manufacturing process, revealing the step-by-step journey from raw materials to the stunning finished product.
Table of Content
#1 Faucet Manufacturing Process – Research & Development
The R&D faucet manufacturing process helps develop faucet design, technology, and functionality to ensure that faucets remain reliable, efficient, and consistent with changing consumer needs and preferences.
#2 Faucet Manufacturing Process – Sand Core
The sand core faucet manufacturing process can create complex functional designs while maintaining the faucet exterior design. Luxuryhome has its own sand core process and can provide OEM and ODM services to our customers.
The following are the main characteristics of the faucet sand core process.
#3 Faucet Manufacturing Process – Gravity Casting
Gravity casting is a faucet manufacturing process for the production of faucet parts or other metal products. Molten liquid metal is poured into a reusable mold, Under gravity’s influence, the metal will flow into the set mold, a process also known as gravity die casting or permanent mold casting.
Gravity casting is the preferred choice for producing faucet components with intricate details, internal passages, and complex shapes that are difficult to achieve through other manufacturing methods.
The gravity casting faucet manufacturing process allows manufacturers to produce high-quality faucets or components with consistent dimensions and finishes while balancing precision, efficiency, and economy.
#4 Faucet Manufacturing Process – CNC Machining
In the faucet industry, CNC machining is a widely used faucet manufacturing process that uses computer-controlled machines to process faucet components.
CNC stands for Computer Numerical Control, and CNC machines are programmable devices that follow coded instructions to perform machining operations.
Suitable for a wide range of materials, including metals such as brass, stainless steel, and aluminum, as well as plastics and composites, and the automation of CNC machining reduces the risk of human error.
#5 Faucet Manufacturing Process – Polishing
The polishing process is a key step in faucet manufacturing that improves the appearance and surface quality of faucet components.
The goal is to polish away any sharp edges or burrs, remove oxidation and stains from the metal surface, and restore the original luster of the material.
#6 Faucet Manufacturing Process – Electroplating
Electroplating is a method of applying a thin layer of metal to the surface of a faucet component to improve appearance, enhance corrosion and abrasion resistance, and protect the surface appearance of a faucet or other product.
#7 Faucet Manufacturing Process – Water Testing
Water testing is a quality inspection of faucet manufacturing that tests faucets for leaks at different water pressures to ensure that each faucet is 100% leak-free, and also tests for longevity and durability under various conditions of use.
Problematic faucets can be quickly identified and reworked.
#8 Faucet Manufacturing Process – Assembling
The assembly process is also a key stage in the faucet manufacturing process where components are put together to form a fully functional faucet or another product.
We use the best components in the industry, like the Sedal cartridge, Kerox thermostatic cartridge, Neoperl’s aerator and supply line, and so on.
#9 Faucet Manufacturing Process – Packing
Packaging is the final step in the faucet manufacturing process for distribution and delivery to consumers to ensure that the product is intact even in poor transportation conditions, good packaging will also attract the attention of consumers and increase their desire to buy, want to customize color box packaging for free? Please contact us.
Good packaging combines protective measures with brand appearance and leaves a positive impression on customers, strengthening brand and marketing impact.
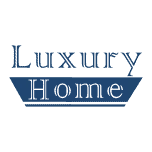
About Luxuryhome
Luxuryhome is not just a faucet manufacturer or wholesaler, but more like a partner who can provide you with more added value.
We are united in our determination to produce China-made bath and kitchen fixtures adhering to the highest ethical principles. You have our promise!
More post you may interested in